top of page
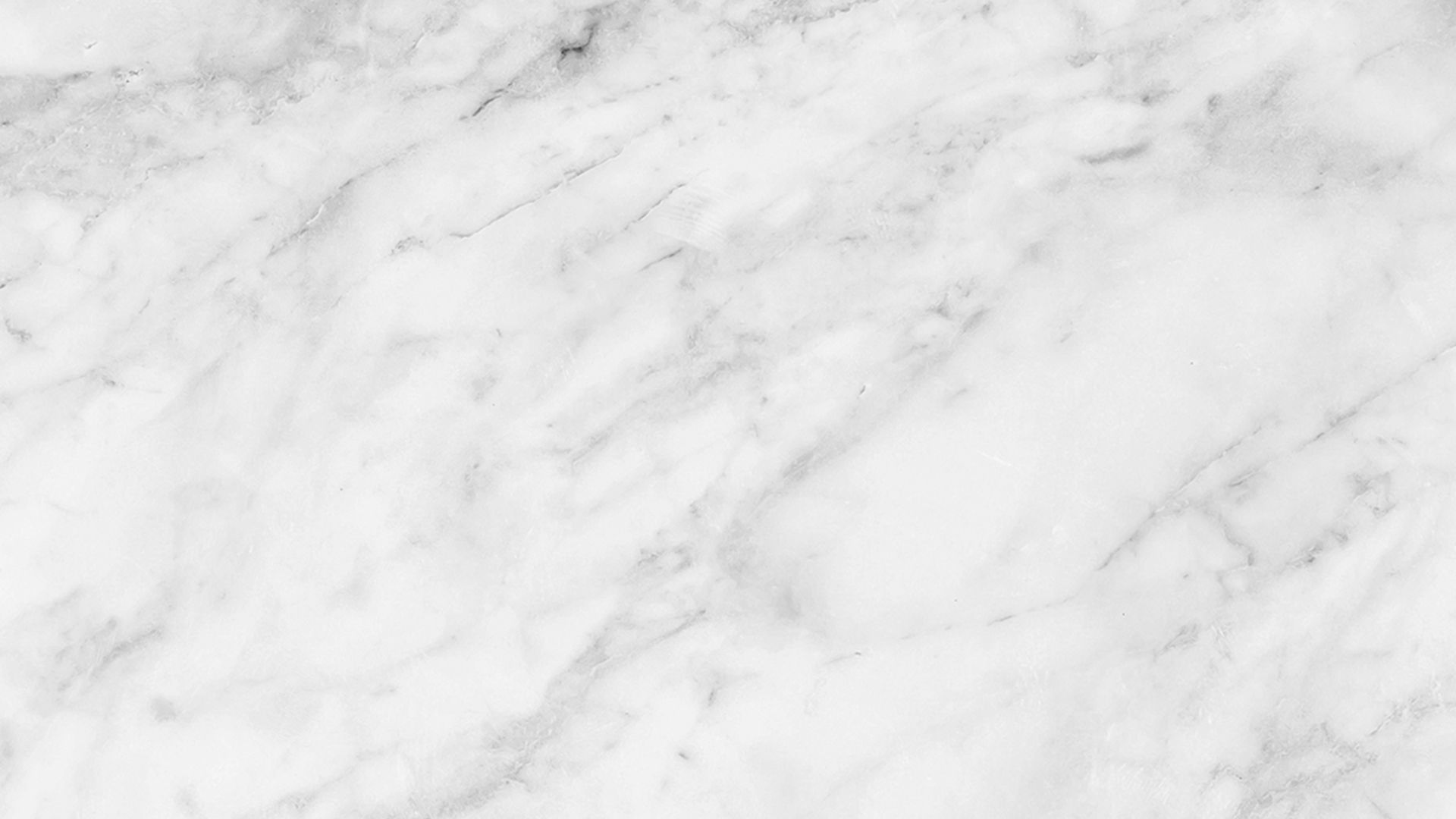
Project on Double Pipe Heat Exchanger (Oct 2017 - Jan 2018)
The main goal was to produce a double pipe heat exchanger (DPHTX) according to the problem statement with an appropriate number of pipe layers to meet the thermal and hydraulic demand and to serve the domestic application efficiently. The problem statement also prescribed us the materials needed to be used for the tubes. The inlet temperature (90° C) and the outlet temperature (45° C) were also descripted there. Fouling action was taken into account on both the pipe sides. We were given a value of heat duty and a double pipe heat exchanger were designed while keeping in mind the impacts of pressure drop and mass flow rates on both of the tubes. After we determined the dimensions for the design, our next task was to produce a 3D model of the heat exchanger. Our team used SolidWorks 2013 for this purpose. We created a 3D drawing, then we prepared a scaled down model of the heat exchanger. While designing and calculating, our fundamental goal was to achieve the greatest values of heat transfer coefficients on the both sides. The overall heat transfer coefficient were found via several iteration. After selecting an optimized design, the next task was to carry out the detailed mechanical design of the entire heat exchanger for a suitable real-life case. I, along with my friends Shamim Afsan, Jahid Hasan Sumon, Saad Junayed performed the work in our machine laboratory.
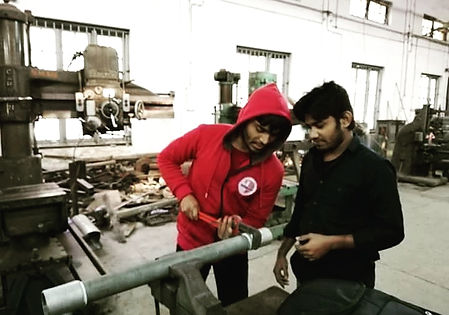
Image: Me and my project partner Sumon working in the pipe setting


Image: SOLIDWORKS design
Project Data and Calculation

bottom of page