top of page
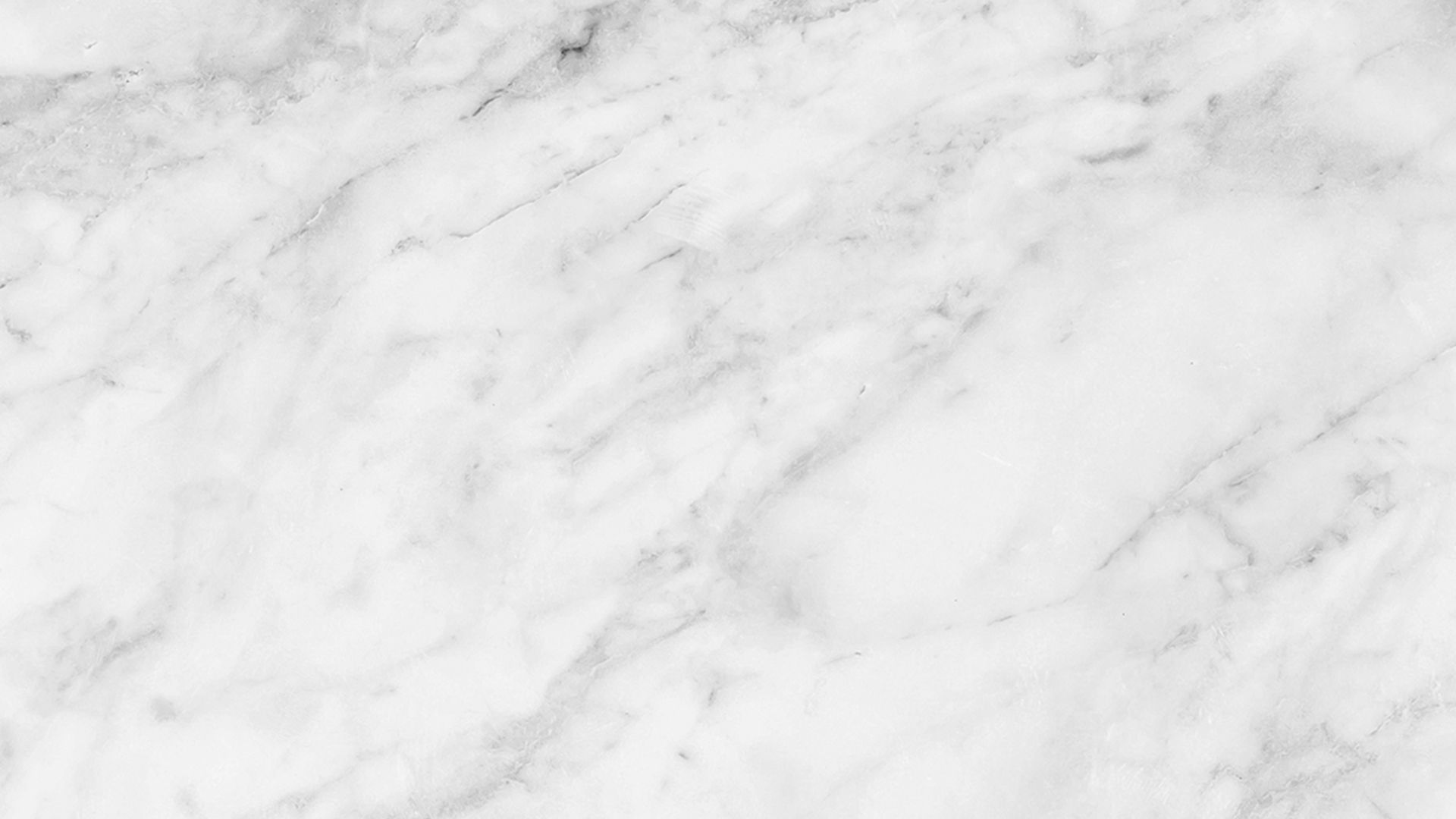
Finite Element Analysis of Automobile Leaf Spring
December 16, 2020 - March 11, 2021
Abstract. Leaf springs are special kind of springs and is one of the most important components of an automobile suspension system. Leaves are basically a series of flat plates, usually of semi-elliptical shape. Generally, a multi-leaf spring used in automobile suspension, consists of two types of leaves i.e. graduated-length leaves and full-length leaves. The advantage of leaf spring over helical spring is that the ends of the spring may be guided along a definite path as it deflects to act as a structural member in addition to energy absorbing device. The main function of leaf spring is not only to support vertical load but also to isolate road induced vibrations. It is subjected to millions of load cycles leading to fatigue failure. Static analysis determines the safe stress and strain of the leaf spring and also to study the behavior of structures under practical conditions. Our present study attempts to analyze the safe load of the leaf spring. It also validates the concept of cantilever beam employed in the theoretical analysis of multi-leaf spring. A lot of research work has been carried out in the context of leaf spring considering its material and a significant progress has been observed in the field of weight reduction, and improvement of load carrying capacity under the replacement with any advanced material. Finite element analysis has been carried out to determine the safe stresses and pay loads. The multi-leaf spring was modeled in SOLIDWORKS 2015 and the same were analyzed under similar conditions using ANSYS Workbench 19.2 software considering structural steel and SAE 1074 spring steel as the spring material. Theoretical and software-based results are presented and compared for validation. Dimensions of the multi-leaf spring are taken from practical understanding.
bottom of page